Shoei : Visite des coulisses
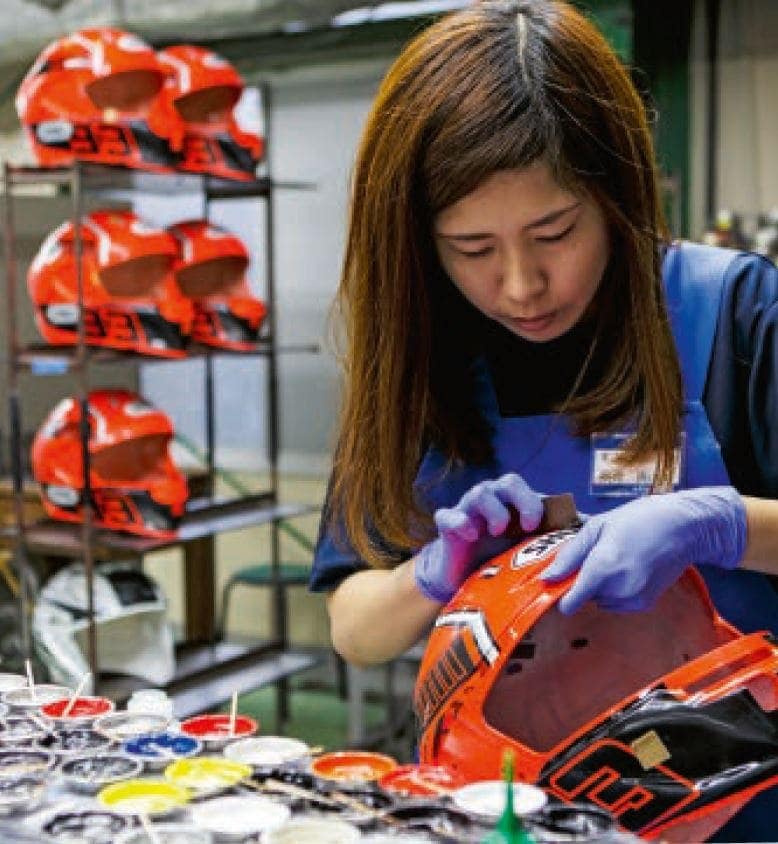
Shoei produziert seit 1958 Motorradhelme. Ist dazu heute überhaupt noch Handarbeit erforderlich? Ja, und zwar überraschend viel, wie wir bei unserem Besuch der beiden Shoei-Werke in Tokio und Ichinoseki erfuhren.
Wie spricht man es eigentlich korrekt aus: Schö-ie oder Scho-ei? „Scho-eh, lautet die korrekte Aussprache“, meint Shoei-Mitarbeiter Naoki Fukui, der uns am Flughafen Tokio-Haneda abholt. Es ist ein Samstag im Jahr 2019, und weil in Japan sechs Tage die Woche gearbeitet wird, ist die Metro ähnlich stark frequentiert wie werktags in einer europäischen Grossstadt. Wir sind sieben Journalisten aus Europa, die in den folgenden Tagen viel über die Produktion von Töffhelmen bei Shoei erfahren werden.
Head-up-Display
Doch am nächsten Morgen besuchen wir erst einmal die „Tokyo Motorcycle Show“, auf der auch unser Gastgeber mit einem grossen Stand vertreten ist. Neben seinem aktuellen Helmsortiment stellt Shoei in diesem Jahr den Prototypen eines Head-up-Displays vor, genannt „IT-HL“. Hierbei wird das System nicht wie beim ähnlich aufgebauten „Nuviz“ aussen am Helm angebracht, sondern am Arm des Fahrers mit einem Klettband fixiert. Eine im Winkel verstellbare kleine Scheibe aus Plexiglas besorgt die Projektion auf die Visierinnenseite. Die Info etwa zum nächsten Abbiegepunkt, zur zulässigen Höchstgeschwindigkeit oder über eingehende Telefonanrufe werden so je nach Einstellung näher oder weiter entfernt ins Blickfeld gerückt.
Infos können ablenken
Auch wir dürfen auf einem Töff Platz nehmen und uns selbst ein Bild auf einem Flachbildschirm machen, der Stadt-, Landstrassen- und Autobahnfahrt simuliert. Erster Eindruck: Die zusätzlichen Infos können vom Verkehr ablenken und bedürfen einer Gewöhnungsphase. Shoei ruht sich also nicht auf der Produktion seiner Premiumhelme aus, sondern arbeitet auch intensiv an der Umsetzung innovativer Lösungen.
Alles beginnt mit einer Glasfaser
Danach steht der Besuch des 1989 erbauten Shoei-Werks im 460 km nördlich gelegenen Ichinoseki an. Zu Beginn der Herstellung eines jeden Shoei-Helms werden für die Aussenschale Glasfiber-Bänder (aus denen Shoei-Helme zu 95 Prozent bestehen) maschinell aufgenommen und zu Matten verarbeitet, die dann mithilfe von vier unterschiedlich grossen 3D-Schablonen maschinell gepresst werden. Zwei Arbeiter kontrollieren nach der Vorformung das Gewicht und sortieren Abweichler aus.
Drei Lagen
Drei Lagen werden nun in eine zweiteilige, der Grösse entsprechende Metallform gedrückt. Unter Zugabe von Dyneema (ein Nylon-Kunststoff) und flüssigem Kunstharz wird das Material auf 120 Grad Celsius erhitzt. So entsteht die Aussenschale, das Grundgerüst eines jeden Shoei-Helms. Weiter geht es mit der Kontrolle der Aussenschale, zwei bis vier nimmt sich ein Arbeiter gleichzeitig vor. Die dafür benötigte Zeit variiert von Modell zu Modell, für den «X-Zero» braucht er zum Beispiel fünfeinhalb Minuten.
Manuelle Verstärkung
In der nächsten Sektion werden spezifische Stellen der Aussenschale manuell verstärkt. Auf Kontrollzetteln an den Schalen stehen alle wichtigen Daten, Modell, Grösse, Bestimmungsland, Datum des Produktionsstarts sowie Montagedatum. So lässt sich jederzeit jede Aussenschale problemlos identifizieren. Modelle, die für das Ausland produziert werden, erhalten zum Beispiel aufgrund der unterschiedlichen Kopfformen – asiatische Köpfe etwa sind runder als europäische – spezifisch geformte Innenleben und Polster.
Hohe Flexibilität in der Fertigung
Hier in Ichinoseki entstehen die Modelle NXR, GT-Air II, Hornet ADV, JO, EX-Zero, RJ-Platinum sowie der VFXWR. In Tokio sind es der X-Spirit III, der Neotec II und der J-Cruise. „Auf jeder Maschine hier wie dort kann aber jedes Modell gefertigt werden, damit bleiben wir in der Fertigung flexibel“, erklärt Shoei-Mitarbeiter Makito Ogawa. Kleinere Abweichungen zum Beispiel bei der Aufnahme der Visiermechanik können von den Arbeitern manuell korrigiert werden, der Ausschuss an Helmschalen tendiert gegen Null.
Laserschnitt
Im nächsten Fertigungsschritt schneidet ein Laser die Formen an der Unterkante und für das Visier sowie die Löcher für die Be- und Entlüftung. Darauf folgt die manuelle Prüfung der Materialstärke, die je nach Zone zwischen 1,3 und 3,5 Millimeter beträgt. Schwarze horizontal und vertikal verlaufende Markierungslinien erleichtern hierbei die Kontrolle. Zu diesem Zeitpunkt wiegt die Aussenschale modellabhängig zwischen 480 und 540 Gramm. Sind alle Parameter erfüllt, erhält sie einen Stempel.
Waschstrasse
Nun durchläuft die Aussenschale eine Waschstrasse, bevor sie in der nächsten Sektion in sechs Schichten glänzend oder matt lackiert wird. Darauf erfolgt eine optische Kontrolle. Wenn es Abweichungen bei der Lackierung gibt, werden die entsprechenden Stellen markiert, in Handarbeit abgeschliffen und bis zu dreimal nachlackiert. Dadurch kann es zu Gewichtsabweichungen kommen, was den Aufkleber auf der Rückseite des Helmes mit der Gewichtsangabe und dem Zusatz „+/– 50 g“ erklärt.
Dekorfolie
Nächster Schritt: Dekorfolien auftragen. Dafür werden zuerst manuell die dazu notwendigen Fixierpunkte markiert, danach die Dekorfolien in Wasser vom Trägermaterial gelöst und von Hand auf die zuvor bewässerte Aussenschale aufgebracht. Hier ist sehr viel Fingerspitzengefühl gefragt, wir dürfen beim Folieren selbst Hand anlegen und erfahren dabei, wie schwierig dieser Arbeitsschritt ist. Eine Fachkraft benötigt dafür je nach Modell pro Stück 22 bis 40 Minuten. Die Folien sind maximal ein halbes Jahr haltbar, bis dahin müssen sie weiterverarbeitet sein. Shoei-Helme haben keine langen Lagerzeiten.
Innenschale, Futter, Belüftung…
Der nächste Abschnitt sieht unter anderem die Montage per Hand von Innenschale, Innenfutter, Visierund Belüftungsmechanik, Kinnriemen, Sichtlippen, Visier und Sonnenblende vor. Die Präzision, die Geschicklichkeit und das Arbeitstempo, das die Arbeiterinnen und Arbeiter in den einzelnen Schritten den Tag legen, sind beeindruckend. Bevor die Visiermechanik angeschraubt wird, klebt ein Arbeiter ebenfalls in Handarbeit eine angerauhte Trägerfolie auf. Sie soll durch im Fahrbetrieb auftretende Vibrationen hervorgerufene Lackschäden und das Verrutschen der Mechanik verhindern.
Stichproben
In der vorletzten Halle werden die Helme in Stichproben diversen Schlagprüfungen unterzogen. Je nach Verkaufsland unterscheidet sich das hierzu notwendige Prozedere. So gleicht der Schlagprüfstand zur Erfüllung der ECE-Norm mit fünf Schlagpunkten dem uns bekannten etwa beim TÜV Rheinland. Für die in Amerika geltende SNELL-Norm wird ein Metalldorn mit drei Kilo Gewicht aus einer Höhe von drei Metern auf einen beliebigen Punkt geschlagen. Und die Visiere müssen dem Beschuss eines Ein-Gramm-Projektils standhalten, das der Munition eines Luftgewehrs gleicht.
Ablaufoptimierung
„Bis alle Abläufe optimiert sind und ein neuer Shoei in den Standardproduktionsablauf kommt, vergehen Wochen“, wird uns mitgeteilt. Betrachtet man den im Verhältnis überschaubaren Anteil an automatisierten Prozessen sowie den grossen Part, den die Handarbeit ausmacht, erscheint jeder Rappen, den der Hersteller für seine Helme aufruft, auf jeden Fall gerechtfertigt.
Windkanal-Test
Zum Abschluss betreten wir die letzte Halle, in der steht der Windkanal. Ingenieur Shigeru Gouribuchi hat ihn selbst entwickelt und demonstriert mit sichtbarem Stolz seine Funktionsweise und die Messmöglichkeiten. Nach einer kurzen Einweisung nehmen wir nacheinander auf einer Honda NC 700 Platz und dürfen im Windkanal den GT Air sowie seinen Nachfolger GT Air II im direkten Vergleich testen. Speziell die gleichmässiger wirkende und damit auch effizientere Belüftung beim neuen Modell fällt dabei positiv auf. Neben Verbesserungen der Be- und Entlüftung lassen sich durch die Messergebnisse der Fahrsimulationen im Windkanal auch Luftanströmung und Geräuschentwicklung der Kopfschützer weiter optimieren.
Japanisches Autobahnlimit: 100 km/h
Bei unserem Test dürfen wir leider nur maximal 100 km/h simulieren, das entspricht der zulässigen Höchstgeschwindigkeit auf japanischen Autobahnen. Die Bitte nach einer Verdopplung des simulierten Tempos auf 200 Stundenkilometer wird freundlich, aber kategorisch abgelehnt. Sicher ist eben sicher.
SHOEI: HISTORIE UND ZAHLEN
Shoei produziert seit 1958 Motorradhelme, seit 1960 entstehen Helme für den Motorradrennsport. Die Fabrik in Tokio produzierte die ersten Töffhelme, die dem japanischen Industriestandard (JIS) genügten. 1965 liess Honda eine Serie von Shoei-Helmen als ihre Originalhelme produzieren und erhöht damit die Popularität und Bekanntheit der Helmmarke. Die Shoei Safety Helmet Corp. wird 1968, kurz nach der Errichtung der Fabrik in Ibaraki gegründet. Trotz des Erfolgs bleibt Shoei eine relativ kleine Firma mit rund 500 Mitarbeitern. Das Unternehmen liefert die Helme für zahlreiche Rennfahrer, aktuell beispielsweise für MotoGP-Weltmeister Marc Márquez oder Tom Lüthi. In der Schweiz zählen der Allrounder GT Air II und der Touring-Klapphelm Neotec II zu Shoeis Topsellern. In seinen zwei Werken in Japan produziert Shoei täglich 2200 Helme an sechs Tagen in der Woche. Davon entfallen 1300 Helme auf die Fabrik in Ichinoseki, wo 270 Arbeitskräfte beschäftigt sind, und 900 auf das Werk in Tokio mit 200 Arbeitskräften. Im Auftrag der Sicherheit werden jedes Jahr 3000 bis 4000 Helme in Stichproben zerstört. Seit der Gründung der Firma werden alle Helme in Japan entwickelt und hergestellt, der Vertrieb erfolgt weltweit.
Text: Jasper Hutte
Fotos: ZVG